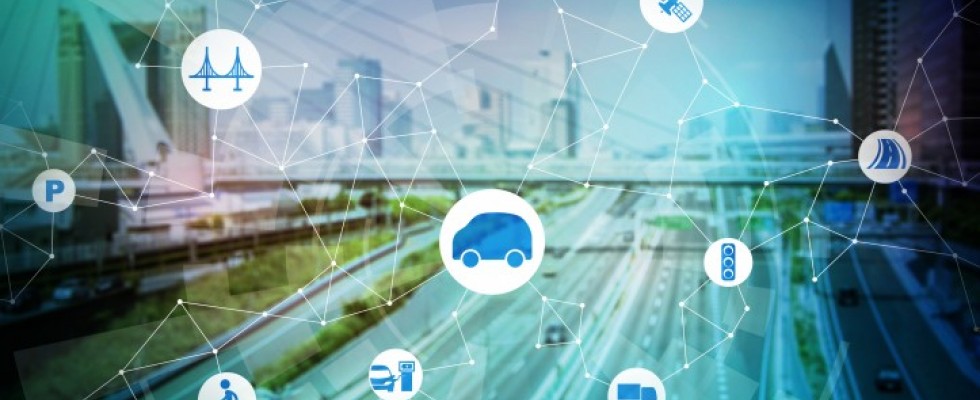
For years home medical equipment providers have relied on outdated, paper-based logistics management solutions to organize deliveries. These models have often resulted in a lack of visibility of delivery technicians, costly write-offs, drivers billing for unexplained overtime hours and sub-standard patient care. Recently though, HME organizations are experiencing significant business improvements by integrating mobile delivery logistics software solutions into daily practices.
From reducing overhead expenses to consistently meeting compliance standards, below are seven reasons why HME providers should take advantage of mobile logistics software solutions to improve business operations and deliver better patient care.
1. Increased Driver Visibility
Gone are the days of the “delivery black hole” where visibility of technicians and their status was a great mystery to dispatchers and management. Implementing mobile delivery logistics software into daily practices enables managers to oversee the location and status of a delivery driver at any given moment in real time. With this increased transparency, organizations are able to ensure the highest level of productivity from their delivery technicians.
Not only does increased driver visibility allow for greater oversight, but it also improves business efficiencies. The ability to supervise and manage a driver’s status at all times reduces the amount of overtime hours and costs that organizations are exposed to. In addition, it also improves customer service, as managers are able to provide an accurate estimated time of arrival to patients.
2. Route Optimization
Similar to increased driver visibility, software with route optimization capabilities improves both field productivity and driver-to-manager communication. As opposed to technicians having to map their own delivery schedules, which can often result in longer transit times and overtime hours, the software does so for them. By imputing all required delivery information, the software determines the most optimal route for a driver to follow, saving time, fuel costs and enhancing on-time delivery.
Additionally, ad hoc orders are quickly scheduled without the trouble of back-and-forth phone calls. Since managers can see what route a technician is on, if there’s a last minute order to fill, they can easily schedule the delivery and the software will automatically factor it into the route.
3. Faster Billing
Typically, HME technicians are tasked with submitting signed proof-of-delivery documents to billing personnel at the end of each day. This paper-based process can be a challenge to manage, often resulting in missing delivery tickets, backed up paperwork and longer hours for those in the billing department.
Utilizing mobile logistics software, on the other hand, automatically files signed documents electronically in the patient file. Not only does this significantly reduce the amount of paper being used, it allows billers to begin the confirmation process for claims submission within minutes of delivery, resulting in quicker payments and reduced overhead expenses.
4. Paperless Environment
The amount of paperwork technicians are required to keep track of can be described as cumbersome at best. From ensuring every signature line is signed to checking that handwritten notes and serial numbers are legible, to submitting all necessary paperwork to the billing department at the end of the day, it’s rarely the case that everything is accounted for.
Due to simple human error, delivery tickets often go missing or signature lines remain blank throughout this process.
Technicians become more organized as mobile logistics platforms store necessary forms on the mobile device for easy access. Additionally, platforms automatically send signed proof-of-delivery documents to the billing department, ensuring nothing gets lost in transit and the order is processed quickly from start to finish.
5. Inventory Management
Maintaining an accurate accounting of items on hand is a crucial component of patient care for HME providers. A recent report from Dobson DaVanzo & Associates entitled “Analysis of the Cost of Providing Durable Medical Equipment to the Medicare Population,” published October 2016, states that 58 percent of the total cost of providing HME services is in the actual prices of the goods. However, with paper-based inventory management systems, it’s difficult to simply view what’s in stock and account for products in the field. Given this significant investment, maintaining and accounting for all inventory, whether in the warehouse, in transit or at patient homes, is key to reducing shrinkage and dreaded inventory write-offs.
For years home medical equipment providers have relied on outdated, paper-based logistics management solutions to organize deliveries.
Mobile logistics software provides an end-to-end chain of custody for inventory without requiring employees to sift through piles of paper. Serialized and lotted inventory items can be tracked easily through bar codes and/or NFC tags, and tied to locations and patients. Not only are managers able to view items in the warehouse, but they can also see what products are in transit and at patient homes or facilities, making inventory reconciliation easier and more accurate.
6. Better Patient Care
From fulfilling ad hoc orders and providing customers with an accurate estimated time of arrival, almost each of the aforementioned benefits have a component that improves overall patient care. When a technician arrives at a patient’s house, their main priority should be to set up the equipment and provide training on how to use it, if necessary.
However, with everything else they must worry about, the time a technician spends assisting the patient is often rushed.
With the ability to optimize the driver’s route and reduce the amount of paperwork to review at each stop, mobile logistics software allows drivers to spend more time focusing on the patient’s needs and less on worrying about signatures and making it to the next location in enough time.
In addition, the enhanced transparency and line of communication between drivers and managers ensures quality care for patients with last minute special requests or orders.
7. Maintaining Compliance and Easy Auditing
Arguably, one of the most important priorities for health care organizations is maintaining compliance and accreditation. Paper-driven logistics management processes can be one of the many reasons why HME companies lose their compliance status because of the vast amounts of missing information and paperwork.
With the system of checks and balances provided by a mobile logistics software solution, technicians ensure they are taking all the necessary steps to meet compliance standards. Additionally, since all records are filed electronically, not only are drivers almost guaranteed not to overlook any procedures, documents are simpler to locate in the event of an audit.